Dust particles suppression in MRO hangar
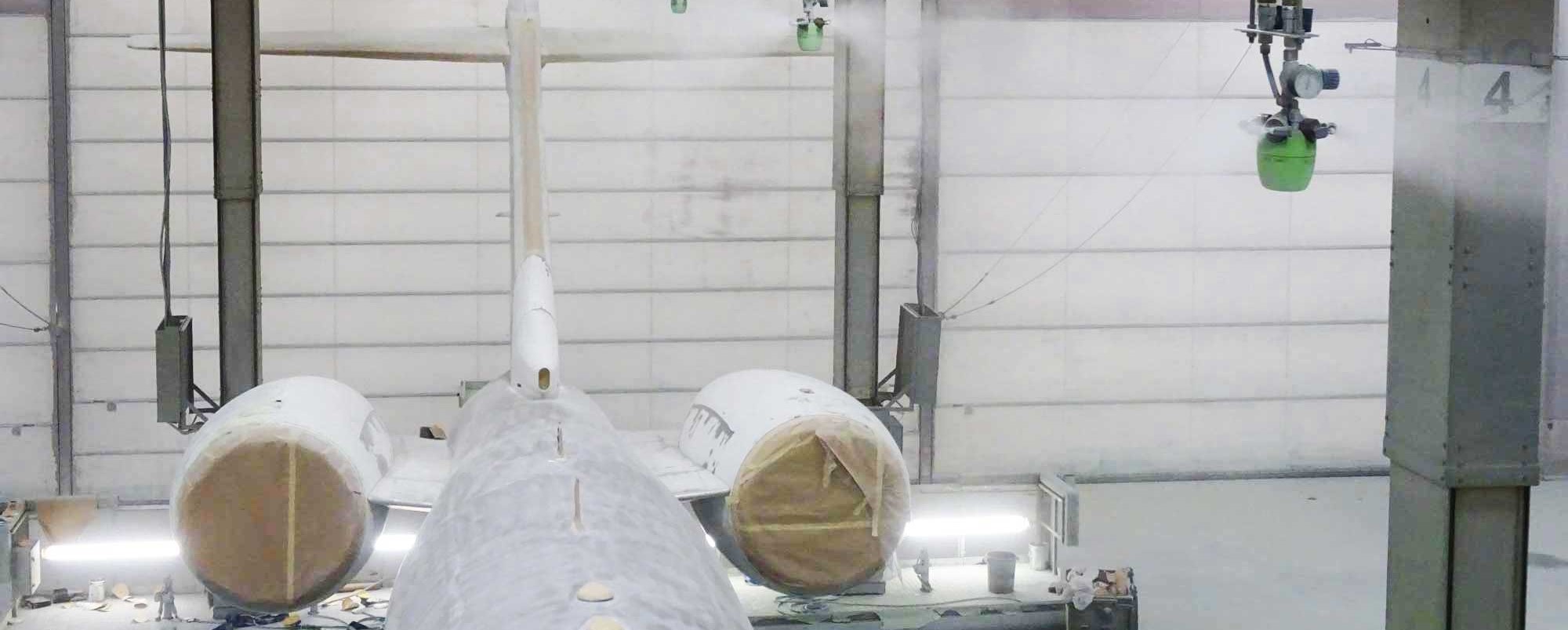
Case Study – How to suppress dust particles in MRO hangar during the painting process?
Issues in MRO paint hangar
Dust particles in an MRO paint hangar can lead to several defects and inconveniences:
- Sanding
- Dust adhesion
- Airborne contamination (sanding dust particles)
- Cleaning costs and time
- Painting
- Paint cracks
- Dust related defects
- Drying time of water-based solvents
- Airborne contamination (paint fumes)
- Repairs
- Repair time
- Long turnaround time
Solution: Dust particles suppression to improve product quality and production
Sanding and painting in the same hangar causes several issues for MRO paint shops, one of them being dust particles in the air. Our systems spray small water droplets in the air during and after the sanding process for dust particles suppression. In addition, we increase the humidity to prevent dust adhesion.
We offer customized solutions adapted to each hangar’s specifications: hangar size, air circulation rate, air flow, existing installation (HVAC), local climate, etc.
AKIMist® “E” SETOJet Version is a dry fog humidifyer which can suppress dust without clogging
- Non-wetting – droplets are as small as fog and evaporate before reaching any surface
- Very energy efficient – 1/5th the energy use of conventional humidification systems
- Easy installation – can be added on to the existing HVAC
- Low maintenance due to anti-clog design
Results after installing AKIMist® “E” SETOJet
- Great reduction in defects and paint cracks as a result of dust suppression
- Productivity increase due to less cleaning time
- Repair time reduced
- Longer lifespan of machinery due to the reduction in dust particles
- Drying time of water-based solvents is reduced