Textile
Warping process
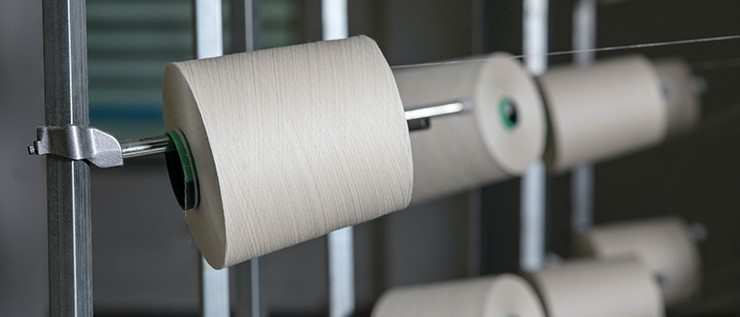
Process
What is warping?
Warping refers to the process of arranging yarns or threads lengthwise on a loom. During warping, parallel threads are wound onto a beam in preparation for the weaving process. This step ensures that the threads are properly aligned and tensioned before weaving.
Issues during warping
A critical point when it comes to warping, is maintaining the preservation of the yarn’s elongation at a constant level. If the warp beam does not consist of qualitative warp yarn, there is a possibility to disrupt the weaving performance.
Types of warping
There are two types of warping:
-
Direct warping
-
Sectional warping
What is direct warping?
Direct warping is also known as beam warping or high-speed warping. This type of warping relates to drafting the yarn from an individual package located on the creel, directly onto the beam. The reason behind direct warping is to develop smaller beams. Furthermore, by combining these smaller beams will result in producing a weaver’s beam.
Problems during direct warping
One problem that occurs with this type of warping is that it generates static electricity. Regardless of the type of material (cotton, wool, synthetic yarn), this causes yarn breakage, it deteriorates the yarn quality, or it even makes the machine stop operating.
What is sectional warping?
The second type of warping is sectional warping. Sectional warping involves two parts:
- warping, and
- beaming.
Here, the incorporation of multiple types of colors in the weaver’s beam is made possible with the assistance of the sectional warping machines. Moreover, beaming refers to winding the yarn on a beam with flanges before the sizing phase.
Solutions
What the advantages of implementing the AKIMist® in the warping process?
As the threads can be fragile during the warping process, moisture plays a major role in ensuring that the quality of the material remains resistant. With the implementation of the AKIMist “E” it is possible to spray “Dry Fog” to establish an optimal level of moisture and relative humidity. By doing so:
- the material maintains the material moist;
- the thread breakage caused by drying is prevented;
- it assist in catching any textile dust;
- and prevents dust from sticking on to the fiber.